There are several ways to generate undercuts in plastic parts. This part is for a military application and required two dovetail features on the A-side of the tooling. To make the design more complicated, the dovetails were in different orientations on two angles.
In a case where there are low annual order quantities, these challenges are easily overcame by hand load tooling inserts. As annual quantities go up, the added cycle time of using hand loads makes investing in automatic actions an easy return on investment. In this case, due to the expected volumes, it was cost-justified to build tooling able to run fully automatic.
To accomplish this, the Basilius team used a floating plate coupled with a cam and groove assembly to pull the dovetail inward as the mold opens. The pictures below show a cut-away of the tooling action. As the mold opens, the cavity side tooling assembly “floats” with the back half of the mold for a brief interval. This action allows the dovetail assembly to retract inward and away from the plastic part. The mold can then open fully with the dovetails removed and the part ready for a normal ejection/robot extraction.
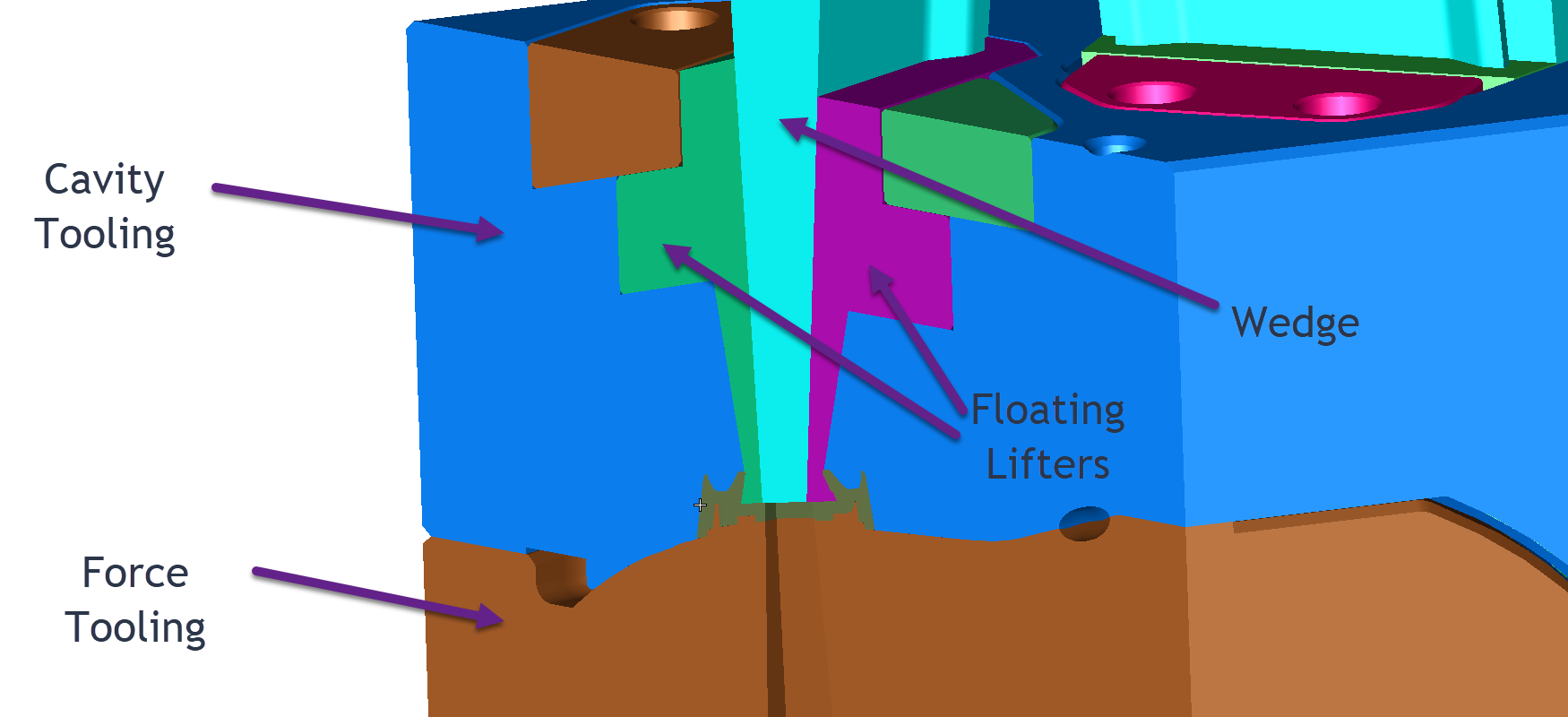
This mold was built to class 101 standard and is a great example of how Basilius used unique but robust design techniques to make a complicated part without adding ongoing labor and cycle time.