As custom molders, we see a lot of part designs requiring metal inserts and overmolding operations. Both of these types of molding involve the same process of loading something into a mold and injecting plastic into or over it to make one complete part. When looking at this as a broad topic there’s almost no limit on what can be overmolded. Even components like electrical connectors, circuit boards, and medical tubing can be overmolded.
Insert Molding
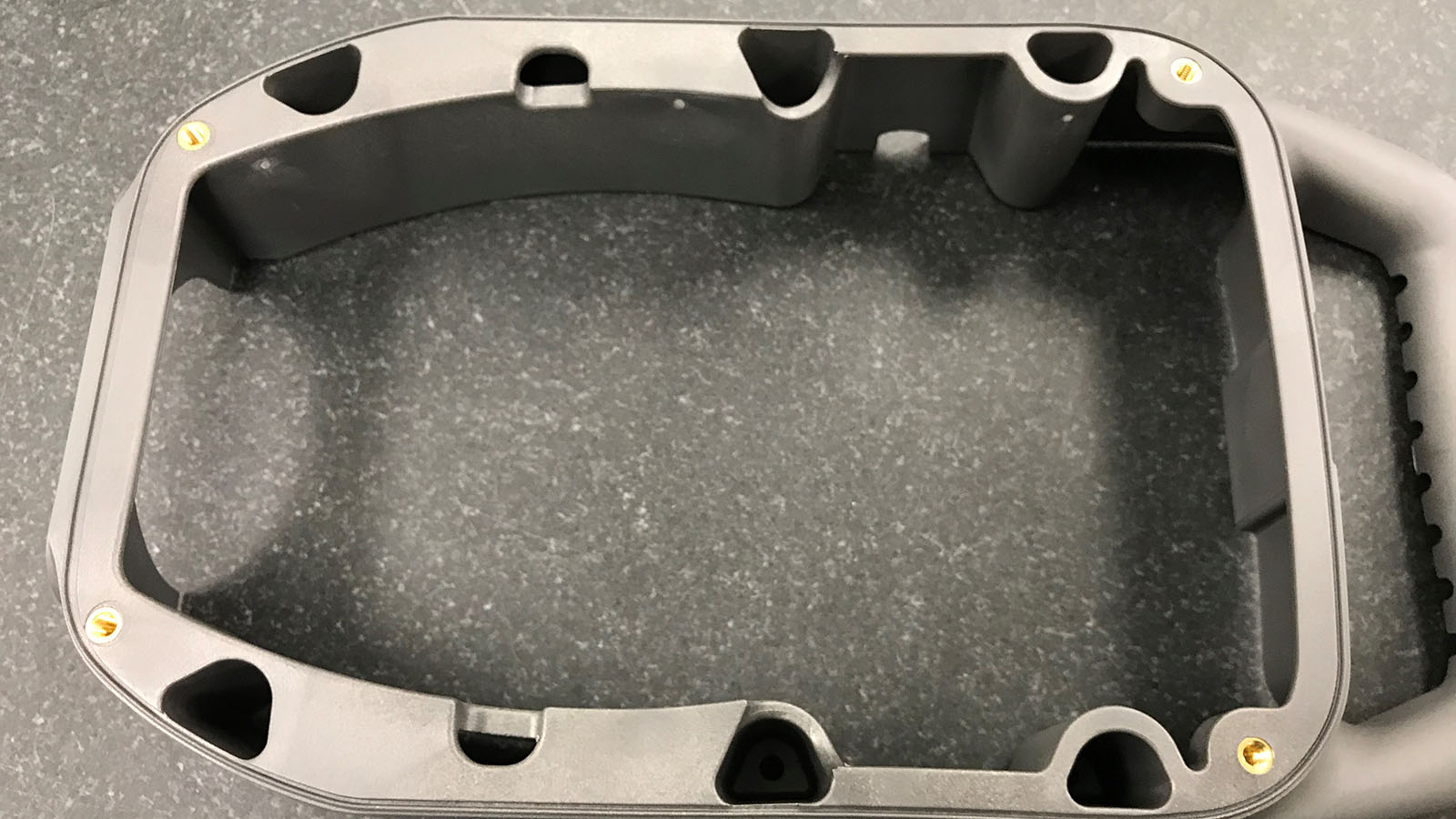
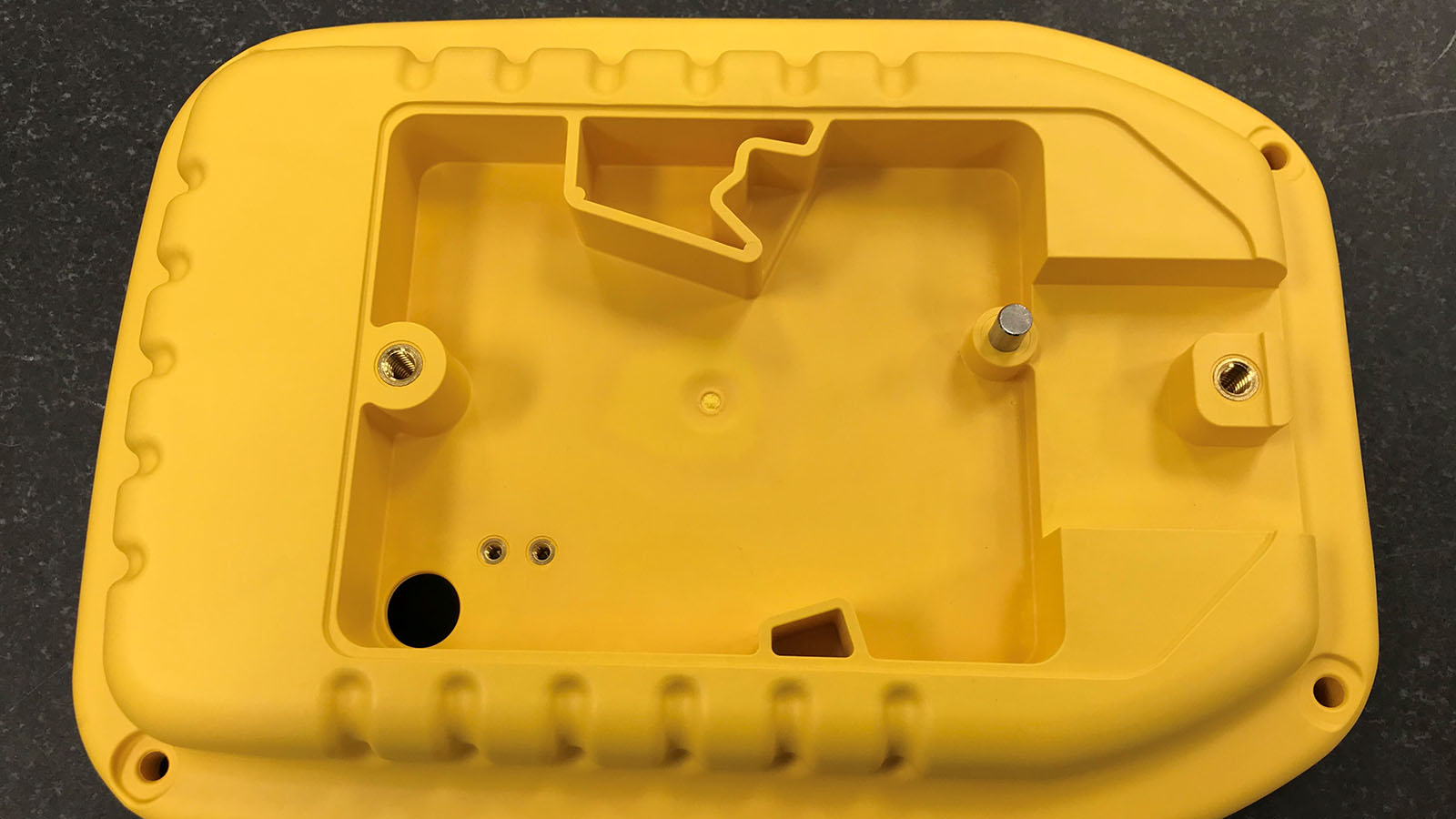
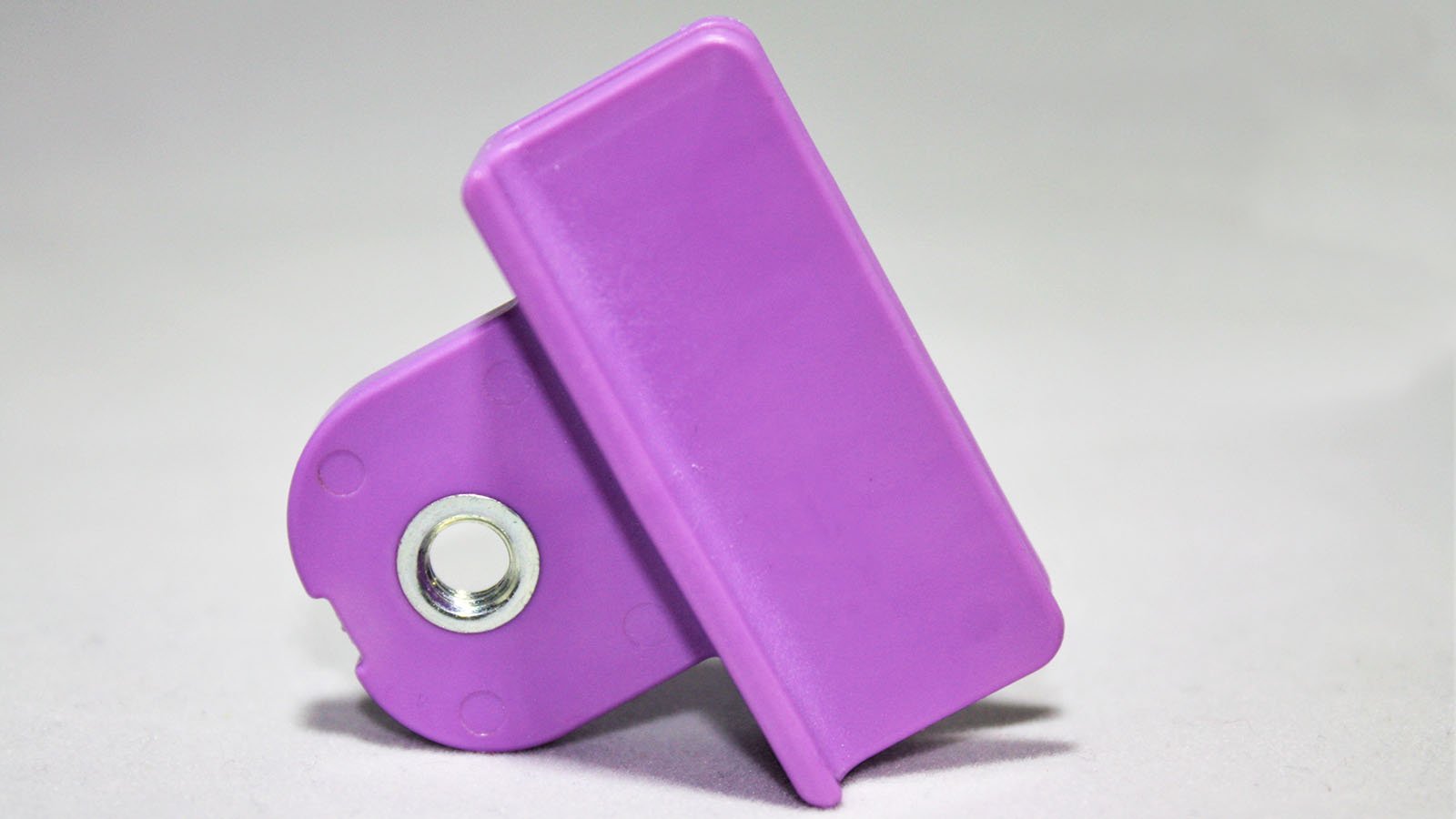
Insert molding begins in the design phase of the mold build. There are two critical design aspects for properly designing an insert tooling design. The first is properly holding the insert, so it does not shift during the injection process. Second is designing so the mold properly shuts off (seals) against the insert. These two aspects make sure the insert is in the same location each time and that no flashing or extra plastic gets molded in the wrong areas.
For example, to hold an internally threaded nut in place we can use a pin that protrudes from the tooling that the insert sits on. The series of images below show the force and support pin of an example mold we’ve built. The next image adds the insert reference, then the cavity side tooling and then the part reference.Depending on the accuracy of the insert, we may use a spring-loaded core pin on one side of the insert. This insert can then compress as the mold closes and allow for any small variations in the insert. In the example above we may take the green core pin and allow a small amount of float (up and down in the image). Some designs may not allow this if the injection pressure would push the pin back.
You’ll notice that the core pins (purple and green) core into each other. The taper of the purple pin is to allow a slight misalignment for operators or robotics when loading the inserts. When using robotics, we may also use docking pins for end of arm tooling to make sure the inserts are accurately located onto the pins in the mold. The injection molding process does not usually change for insert molding. We are still going to develop a process in the same manner, but there could be some other considerations.
When we are adding one or many inserts into the mold, we may need to allow for extra cycle time whether the components are loaded by robotics or by hand. Some cost implications for the insert molding are not only the insert itself but how it is loaded. For low volume applications, we can have a full-time operator. For automated systems, there could be some additional up-front costs associated with equipment like robotic tooling or orientation equipment like bowl feeders. This is another aspect of custom injection molding that is taken on a case by case basis. Like with choosing cavitation, we need to balance up-front investment with long term piece price savings.
See more about Insert Molding….
Overmolding Plastic Substrates
Overmolding Other Components
The applications for overmolding are seemingly endless. We can create features like threads, standoffs, and dowels by loading these inserts into a molding machine prior to molding process. Looking at the topic more broadly we can mold plastic over just about anything. From traditional applications like adding ergonomic grip points to more advanced electronics or medical devices, it’s all in the realm of possibility. These applications may even provide cost savings opportunities for component assemblies by avoiding secondary operations.
This post is part of our Designing for Injection Molding series. Check out more here.