Almost all CNC component needs to interface, connect, or interact with other components. Making sure that the interface connects accurately and repeatedly is where tolerances come into play. Creating prints with tolerances eliminates the guesswork for the machine operator. The image below shows an example of a hole that, without tolerances and callouts, could be open to interpretation.
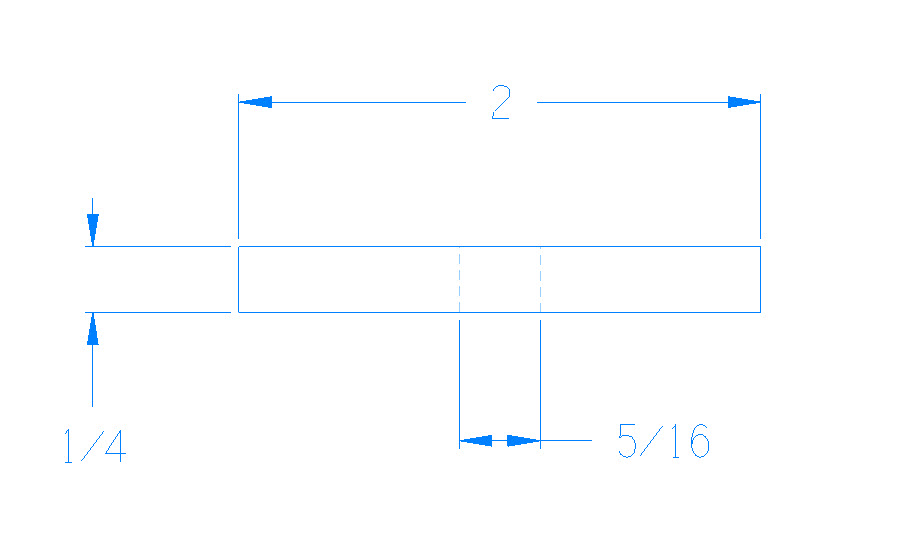
You can see that the hole is labeled as 5/16. To a machine operator, that could mean a clearance drilled hole for a 5/16 bolt, a 5/16 dowel, or even a 3/8-16 tapped hole. Let’s say the hole was for a dowel pin that needs to be easily removed (slip fit). Adding a dimension with tolerances (.313 +.0005/-.0000) shows the operator that the hole needs to be slightly oversize to allow the slip fit. Adding a callout like “Slip fit to standard 5/16 dowel pin” gives the operator further understanding of the part. The dimensions and tolerances should remove any assumptions a machine operator could make, but callouts are also helpful.
Tolerances are also important relative to mating components. Shown below are two CNC turned components interfaced by two bearings. According to the drawing for the bearing (shown below) the tolerance on the inner diameter (fit to the shaft) is +0.0000 / -0.0003 and the outer diameter (fit to the housing) is +0.0000 / -0.0005.
Since the tolerance of the bearings (colored blue) is set by the manufacturer, we want a tolerance on the mating components to function properly at the high and low end of the tolerances, for both the bearing and CNC machined component. In this case we want the low-end tolerance of the bearing housing (red) to not go below 2.000. That means the bore for the bearing should be something like 2.000 +0.0005/-0.000. The shaft (gray) needs to fit the ID of bearing. In this case, the bearing could be as small as .9997. Therefore, a tolerance on the shaft diameter of .9997 +0.000/-.0005 would work. Bearings may have unique circumstances where interference is possible or required which can be accomplished in the same manner using tolerances.
Sharp Edges / Burs
For the simplicity of 2D drawings and 3D CAD data, sharp edges are commonly designed into parts with the understanding that they do not necessarily need to be sharp. We assume that parts can have a “corner break” of at least .005 (unless otherwise specified in the drawing) to eliminate the sharp edges. The corner break makes parts easier to handle and also removes burs that could be generated during the different CNC operations. Most 2D drawings will have a callout stating, “Unless otherwise specified, corner break all edges .XXXX”.
Parallelism / Perpendicularity
Parallelism and perpendicularity are common tolerances to overlook. For assemblies, parallelism (or a lack of it) can cause problems that get intensified by distance. For example, a bearing mount for a shaft with only a half degree of misalignment can cause a much larger misalignment at the end of the shaft. The image below is the same part from above tilted .5 degrees, simulating the head of the bearing housing when it is machined out of parallel. You can see that at 11 inches the shaft would be misaligned by almost an 1/8 inch.
Cost Implications
As you can see, tolerances are important for CNC machining operations to ensure consistent part quality. It’s also important to understand what areas or features of your component matter and which ones do not. For most tolerances on prints, only critical tolerances (like the bearing example above) will be labeled. Other dimensions will be specified but will not have tolerances. Instead, there’s typically a call out on a print specifying general tolerances based on the number of decimal places a dimension is showing. For example if a dimension is showing three decimal places (X.XXX) it has a tolerance of +/-0.005.
The purpose of tolerances is also to show the machine operator what matters and what doesn’t (relatively speaking). They can focus on critical areas and may even program the CNC machine in a way that ensures the accuracy and consistency of those dimensions.
Tolerancing areas to be less critical also helps reduce the cost of the part. For example, if every dimension on a print is specified to be +/-.0001, machine operators will have to be careful to maintain that level of accuracy. These dimensions will all need to be confirmed to be accurate, set-up time could be longer, and the programming may need to be modified to run more slowly or make repeated movements. All of which add time, which adds cost.
When setting tolerances, it’s also important to consider how a dimension can be confirmed once the part is complete. For example, setting tight tolerances on complicated contours may require difficult checking procedures or require interpretation from other dimensions. That’s not to say that setting tight tolerances should not be a priority, it’s that setting tight tolerances on areas that don’t actually require it takes extra time and may increase the cost of the part unnecessarily.
Check out this page for more information on designing for CNC Machining.